Safety First: Best Practices for Warehouse Employees
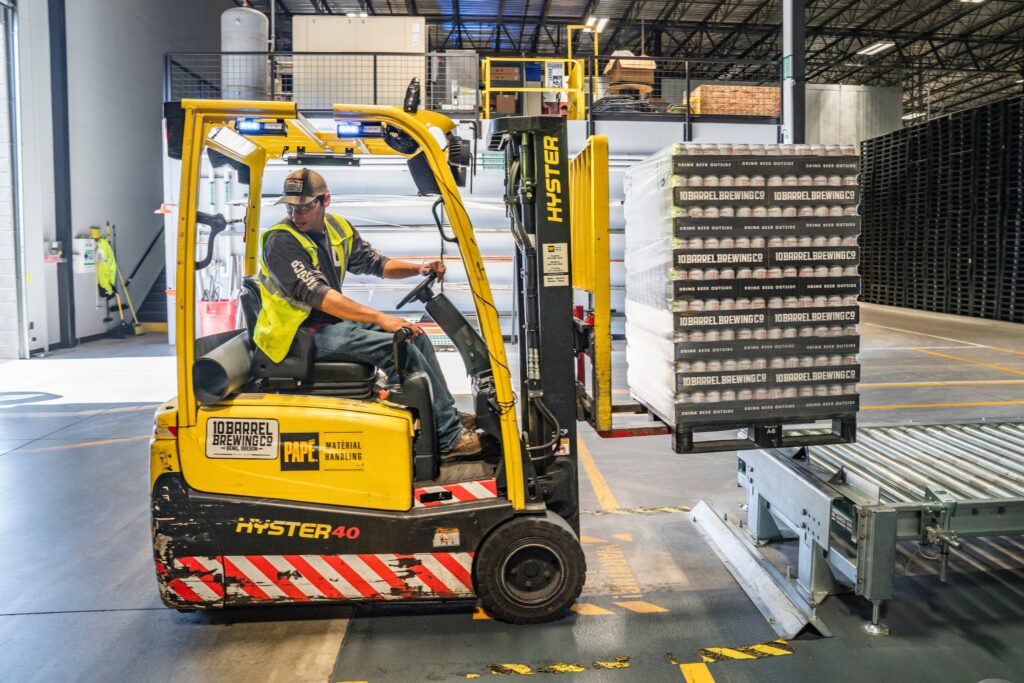
Warehouses are bustling hubs of activity where goods are stored, sorted, and distributed to various destinations. While they play a crucial role in the supply chain, the fast-paced nature of warehouse operations can lead to potential safety hazards for employees. Implementing safety measures is vital to protect employees from accidents and injuries. The following are several best practices for warehouse employees to ensure workplace safety:
- Proper Use of Personal Protective Equipment (PPE): Employees must be provided with appropriate gear, such as hard hats, steel-toed boots, high-visibility vests, gloves, and safety goggles, and shown the correct and effective way to wear them. PPE helps safeguard workers from potential hazards like falling objects, heavy machinery, or chemical exposure.
- Comprehensive Training Programs: From new hires to seasoned veterans, everyone should receive training on equipment operation, safety protocols, and emergency procedures. Regular, up-to-date training sessions should be implemented to keep employees informed about the latest safety standards and best practices.
- Equipment Maintenance and Inspection: All equipment, including forklifts, conveyor belts, and pallet racks, should undergo regular upkeep and inspections. A proactive maintenance schedule helps identify and rectify potential issues before they lead to accidents. Encourage employees to report any malfunctioning equipment promptly.
- Safe Material Handling: Education on proper lifting techniques can prevent strains and injuries. Encourage the use of mechanical aids like forklifts, pallet jacks, or conveyor belts whenever possible to reduce manual lifting. Also, employees should be careful when stacking items to prevent collapses or falling objects. Additionally, if the warehouse deals with hazardous materials, employees should receive specialized training for their proper handling and storage. This includes understanding safety data sheets, chemical labeling, and proper containment measures.
- Organized Workspace: Regularly inspect and clean the facility to remove potential hazards like spills, debris, or obstacles in walkways. Clearly mark designated storage areas, emergency exits, and fire extinguisher locations to facilitate easy navigation during emergencies.
- Respect Safety Signage: Ensure employees understand the meaning of various signs and symbols used in the warehouse and obey them diligently. Whether it’s warning about high voltage, no-entry zones, or restricted areas, adhering to these signs can prevent accidents.
- Fire Safety Precautions: Warehouse fires can be devastating, posing risks to employees, goods, and the facility. Installing smoke detectors, fire alarms, and fire extinguishers throughout the warehouse can prevent disaster. Practice regular fire drills and evacuation procedures.
Workplace safety should never be compromised in the fast-paced environment of a warehouse. By adopting these best practices, employees can create a safe and secure work environment, reducing the risk of injury and accidents. Remember, safety is a cooperative effort, and active participation is crucial to ensuring that safety always comes first!
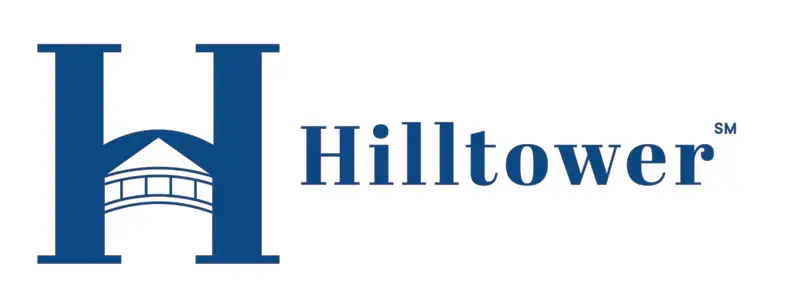